
Seeming to float free, the lace-like facade appears ethereal and delicate. A world first, the woven fibre structure is appropriately innovative for Texoversum, the new textile-focused teaching and research facility that it wraps at the Reutlingen University of applied sciences in Germany.
The facility’s industrial design makes thoughtful use of the enveloping textile as both organizational strategy and interior finish; staircases and collective seating areas crisscross the open and functional split-level floor plans, and a multi-storey mural of vibrant gradients links them all together. “Our mission for each of our projects is to develop a contextual dialogue with the spatial circumstances,” explains Sebastian Thomas, architect and head of project planning at Munich-based Allmannwappner, the firm that took on lead role as planner and architect for the building and its interior. “The building combines different special aspects to develop an identity for the site and the users.”
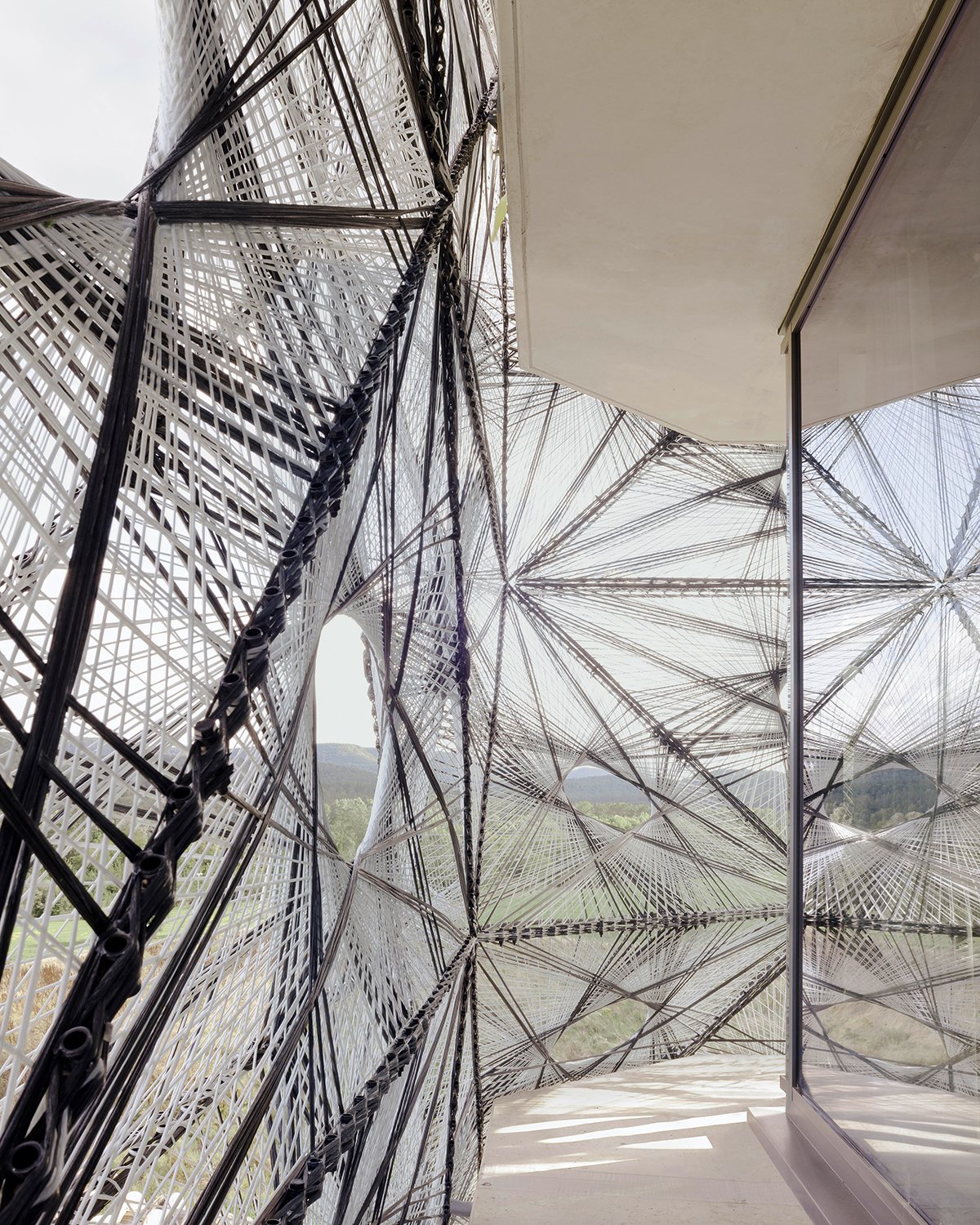
As the most visible external aspect of that identity, the spectacular fibre-composite facade adopts the textile as a literal architectural component. The construction technique is the culmination of years of experimentation and development at the University of Stuttgart by professors Achim Menges and Jan Knippers, who executed the facade system in collaboration with Allmannwappner through their respective firms, Menges Scheffler Architekten and Jan Knippers Ingenieure.
The web-like form consists of outwardly identical triangular tiles with five different inner fibre body templates spanning up to four metres in length (plus two trapezoidal corner elements), which were constructed using a robotic coreless filament winding process (pioneered and developed at the University of Stuttgart) that freely places fibrous filaments between two rotating winding scaffolds; the interaction of these filaments results in the predetermined shapes without the need for moulds or a core. “The carbon fibres have roughly the stiffness of structural steel and take on the main part of the loads,” explains Knippers, “while the glass fibres are significantly weaker and serve primarily as a mould for the carbon fibres.” When assembled from these panels, the fibre composite system can create dramatic shapes without generating any additional waste through formwork.
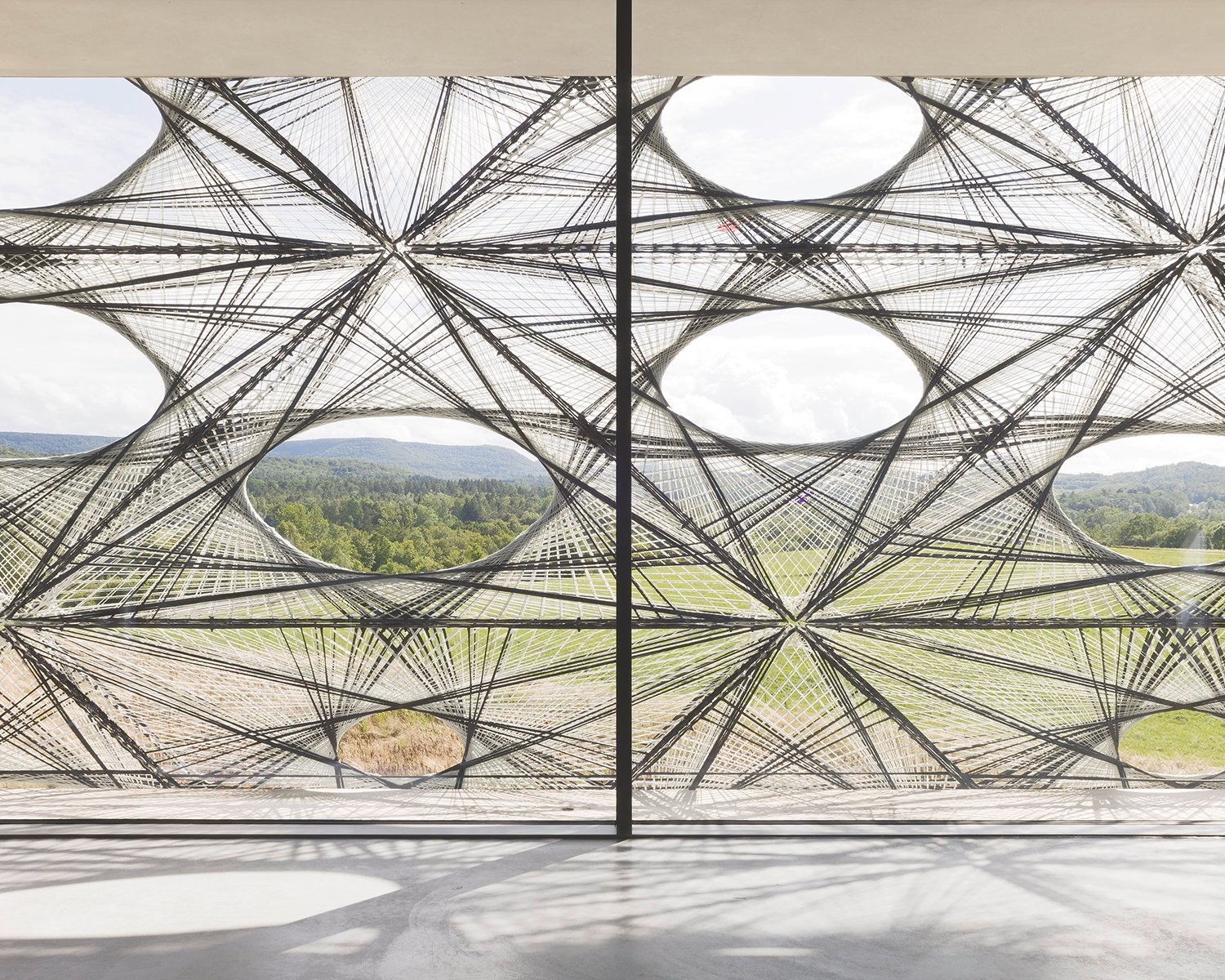
Wrapping Texoversum in the repeating five tiles did present a few challenges. “We had to meet the very strict requirements of the German building authorities and conduct many tests on durability, load-bearing capacity and fire resistance. We adapted the resin to meet these requirements,” says Knippers.
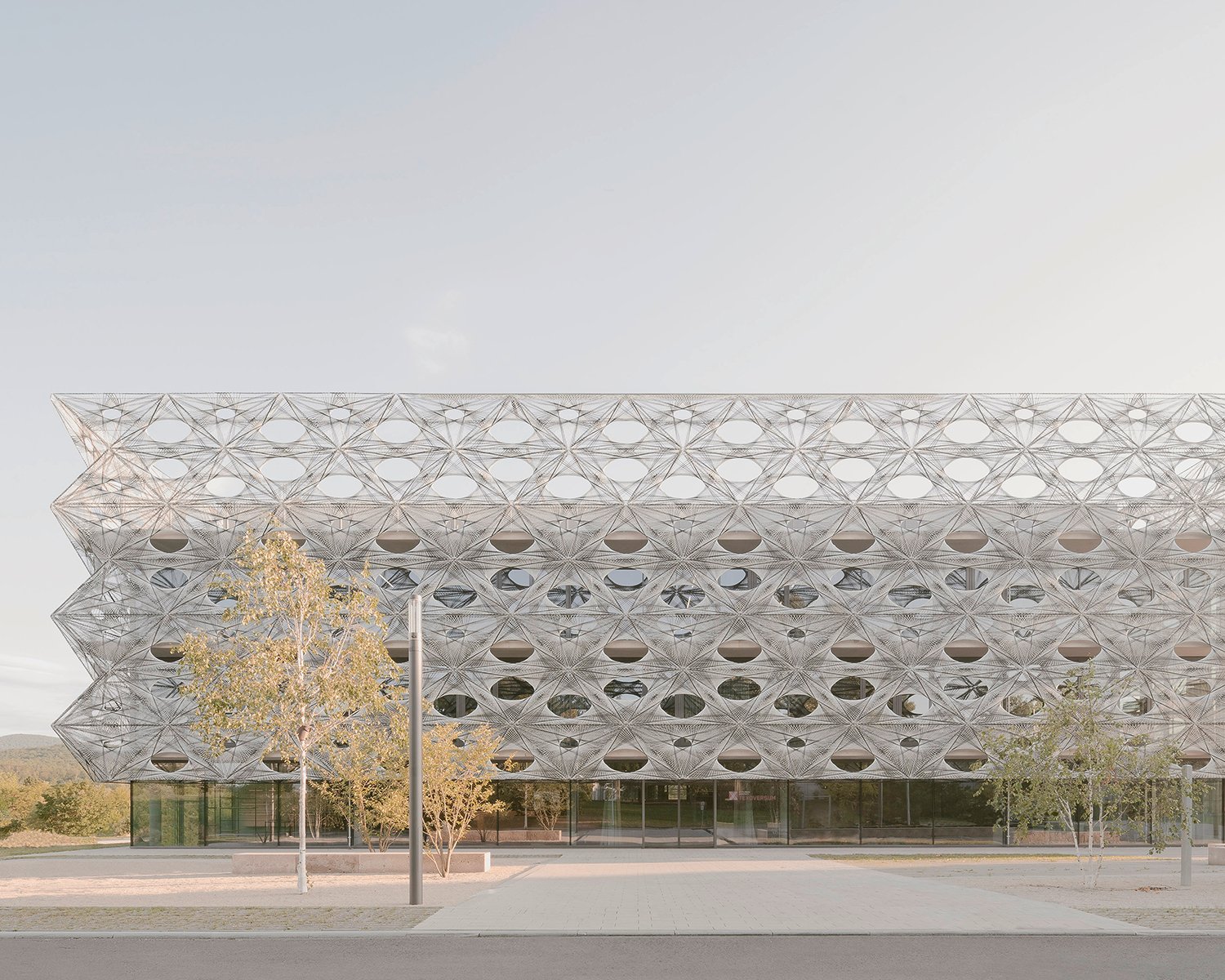
The sculptural facade is more than an expression of the program within. “It constitutes the external sun protection of the building, which has to fulfil stringent shading requirements in compliance with the German building code,” explains Menges. “In addition, the self-supporting fibre elements provide the structural balustrades for the balconies and frame the view towards the surrounding landscape.”